Construction involves multiple stakeholders, including clients, architects, engineers, contractors, subcontractors, suppliers, and operatives. The success of any construction project depends on the effective processes, cooperation and coordination of all these stakeholders.
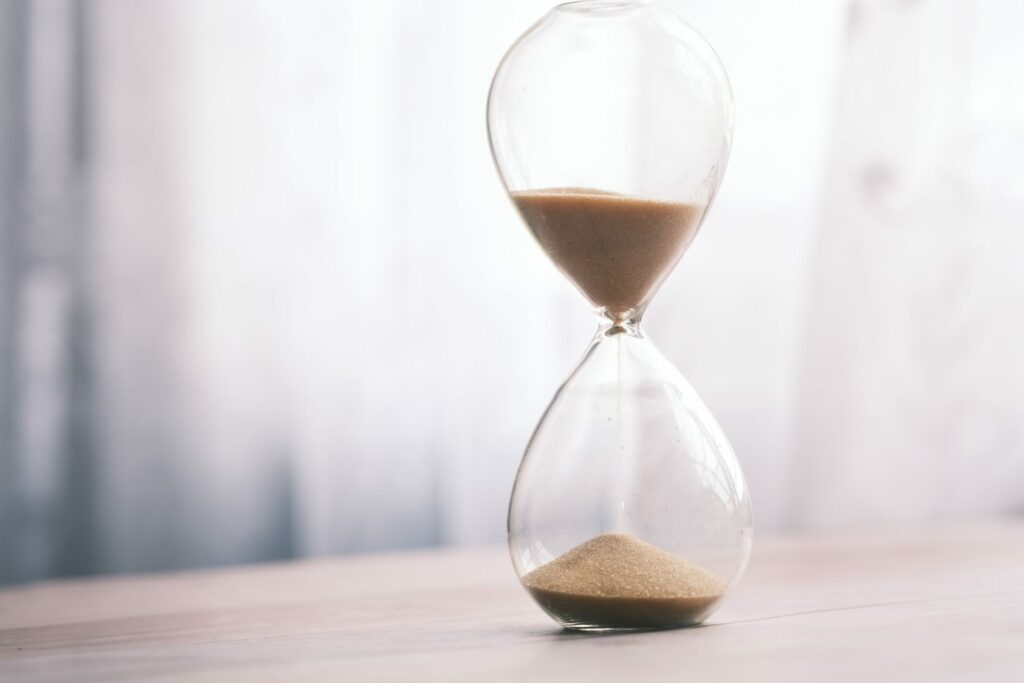
The Price of Time is Higher Than Ever
One of the major challenges facing the construction industry is the high rate of waste, including loss of time, materials, and resources. Not only does this waste lead to cost overruns, but it can also delay project timelines and affect the quality of the final product.
The price of construction time is higher than ever due to increased interest rates, wages and other costs. Therefore improvement of HOW we manage the construction process and improvement of flow on the site is critical.
Applying lean methods with the proper techniques and technology will reduce wasted tool-time, improve the construction process, and increase margins. Sounds good, right?
Lean – What Does it All Mean?
A lean methodology is a systematic approach to eliminating wasted tool-time and increasing the efficiency of the construction process.
The approach identifies and eliminates non-value-added activities and streamlines workflows to increase productivity. By reducing wasted tool-time, Lean methods allow construction teams to complete tasks faster with fewer resources and higher quality.
The adoption of Lean principles is not limited to the construction industry, where its adoption has been steadily growing; it is already widely used in manufacturing, healthcare, etc.
Some Key Principles of Lean Methodology
Continuous Improvement
Continuous improvement means that construction teams should always look for ways to optimise workflow, eliminate waste and increase productivity. This can be achieved by regularly monitoring and analysing the construction process, identifying areas of waste and inefficiency, and implementing corrective actions.
For example, construction teams can monitor the time spent on each task and identify any delays or bottlenecks. By resolving these issues promptly, teams can increase efficiency and reduce wasted time.
Just-in-time (JIT) Delivery
JIT delivery is based on three elements:
- The pull system
- Takt time
- Continuous flow
JIT involves delivering just the necessary materials, tools, equipment, and resources to the construction site exactly when needed. This reduces the need for storage space, reduces the risk of damage or theft, and reduces waste.
Technology and Lean Construction
Using technologies such as Building Information Modelling (BIM), Radio Frequency Identification (RFID) tags, cameras and machine vision, and Bluetooth Low Energy (BLE) technology help facilitate JIT delivery. Real-time situational awareness based on data and visual management is a critical factor in this context.
BIM – a Digital Model of a Building
BIM allows construction teams to create a complete digital model of a building, including all systems and construction parts. This model can be used to plan the build process and ensure all resources are available when needed.
Tracking Progress With Technology
RFID tags, BLE technologies, cameras and machine vision can be used to track progress on site and the movement of materials, tools, equipment, and resources in real-time, allowing teams to monitor their location, status, and usage. Wireless sensors for monitoring the condition of concrete strength or air temperature and humidity help insure one of the essential prerequisites – working conditions for the next tasks.
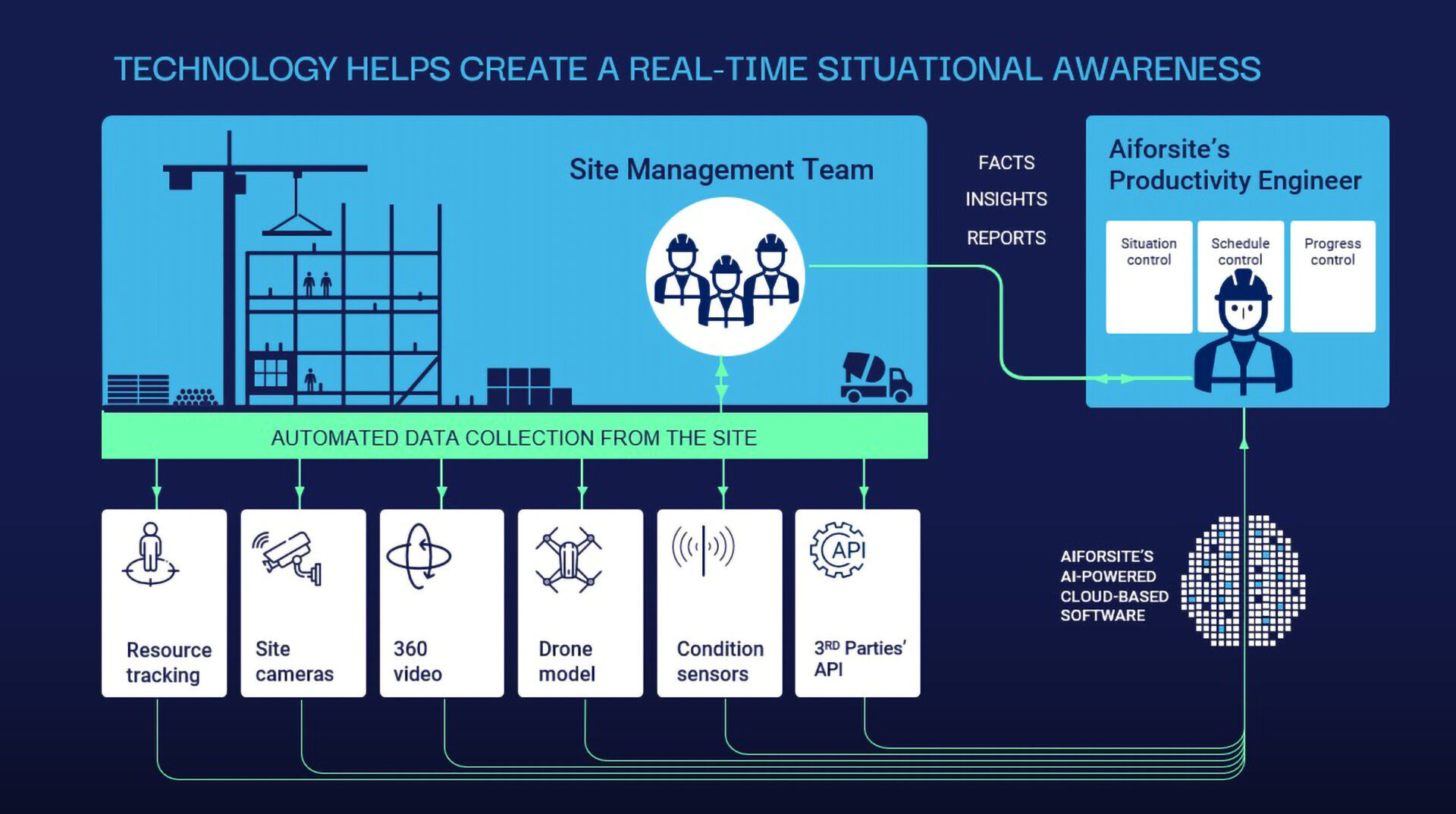
Drones and Robots
Using drones and other automated equipment can also reduce wasted time during construction. Drones can be used for on-site surveys, inspections, and monitoring, reducing manual labour and improving accuracy.
And we’re now seeing automated equipment such as robotic excavators and 3D printers more readily entering the market. These can also reduce the need for labour and increase productivity.
Off-site Methods
The use of prefabricated components can further reduce wasted time on site. Prefabrication consists of fabricating building elements offsite and assembling them onsite. This reduces the need for on-site construction activities, such as cutting, welding and drilling, which are time-consuming and unnecessary.
Prefabrication can be facilitated using BIM and other technologies, allowing construction teams to design and manufacture components to the required specifications precisely.
Linking Lean Construction to Building Safety Act and Golden Thread in the UK
Reducing wasted tool-time using lean methods and the proper techniques can significantly improve and speed up the construction process without compromising health and safety or quality.
In fact, it can actually improve the culture of safety and the quality of the finished product. And if that wasn’t enough, these technologies can also link directly to regulations like the Building Safety Act and the Golden Thread in the UK. Well-documented and shared quality information improves the health, safety and well-being of construction site staff and building users for years to come.
Author of the blog post: Tom Woodhead, CXO of Aiforsite UK Ltd.